Hello there, aspiring Six Sigma enthusiast! If you’re here, you’re probably looking to get your feet wet in the ocean of Six Sigma knowledge. Well, you’ve come to the right place. We’ve got the perfect guide to help you understand one of the most important aspects of Six Sigma: Process Capability Analysis.
But before we dive deep into this topic, let’s first set the stage right. Six Sigma, as many of you might already know, is a method that provides businesses with the tools to improve the capability of their processes. This, in turn, leads to performance enhancement and variation decrease in business processes, all the while reducing errors and boosting profits.
Now, you might be wondering, “where does Process Capability Analysis fit into all of this?” That’s a great question. In the simplest terms, Process Capability Analysis is a crucial part of Six Sigma that helps organisations understand whether their process is capable enough to meet the specifications or requirements set by customers or stakeholders.
In this comprehensive guide, we will go through the key aspects of Six Sigma and Process Capability Analysis, exploring the roles of different Six Sigma belts and answering some of the most frequently asked questions.
The Six Sigma Process Cpk: Your Key to Consistency
Subscribe to our newsletter!
What is the Six Sigma Process Cpk?
At its core, Cpk, or Process Capability Index, is a statistical tool that measures the ability of a process to produce output within customer-defined specifications. In Six Sigma, Cpk is a critical concept that helps quantify the process performance.
Think of Cpk as your trusty guide in the journey towards process improvement. It provides an estimate of how well your process can produce output that falls within the necessary specifications, even when conditions aren’t perfect.
The Magic of Six Sigma Cpk
What makes Cpk so important in Six Sigma, you ask? Here’s the deal: Cpk is all about ensuring consistency.
In a perfect world, every product or service you offer would flawlessly meet customer expectations. But variation is inevitable. That’s where Cpk comes in. It helps you gauge the potential of your process to stay within customer specifications, even amid unavoidable variation.
Simply put, a higher Cpk value means your process is more capable of producing consistent, quality output that meets customer specifications. On the flip side, a lower Cpk might suggest a need for process improvements.
Cpk in Action
Let’s say you’re manufacturing widgets, and your customers require them to be 5 cm, give or take 0.5 cm. Now, due to various factors like machine calibration, material variation, or even human error, not all widgets will be exactly 5 cm. Some might be 4.8 cm, while others could be 5.2 cm. Here, Cpk helps you understand how well your process can create widgets within this accepted range, giving you insights on areas for improvement.
Diving Deeper: The Ins and Outs of Six Sigma Process Capability
Process capability, much like the previously discussed Cpk, is a vital element in understanding the overall quality and effectiveness of your processes within the Six Sigma framework. Let’s break this concept down further for easy comprehension.
Understanding Six Sigma Process Capability
At its core, process capability is the measurable property of a process to produce output within the specification limits consistently. Essentially, it’s about understanding the ‘natural behaviour’ of your process when it is under statistical control.
In Six Sigma, we use process capability to assess how well a process meets the customer requirements or specifications. A capable process is one that produces most, if not all, of its output within the specification limits.
Process Capability: Why does it Matter?
So, why is process capability significant in Six Sigma? The answer is simple: it’s all about customer satisfaction.
In the world of Six Sigma, we consider a process capable when it can meet customer specifications consistently. Hence, assessing the process capability isn’t just a statistical exercise—it directly links to how well you’re able to meet your customer’s needs.
Think of process capability as your early-warning system. It gives you insight into the areas where your process might not be meeting customer needs consistently, giving you a chance to address the issue proactively before it impacts customer satisfaction.
Process Capability and Six Sigma: The Connection
In Six Sigma, the goal is to achieve near-perfect processes where defects are minimal (that’s where the ‘six’ in Six Sigma comes from – it refers to a process that produces only 3.4 defects per million opportunities!). Process capability is your roadmap to this goal, offering insights into your process’s performance and areas for improvement.
Through the lens of process capability, Six Sigma professionals can pinpoint sources of variations in the process, helping to eliminate defects and improve overall process quality.
Now that we’ve set a solid understanding of process capability let’s dive into the questions that often come up in the world of Six Sigma.

FAQs: Your Burning Questions on Process Capability Answered!
How does Cpk relate to process capability in Six Sigma?
Cpk and process capability are two sides of the same coin in the world of Six Sigma. Cpk, or Process Capability Index, is essentially a statistical measure that provides a numeric assessment of process capability. It gauges the ability of a process to produce output within the customer-defined specifications. In other words, it answers the question: “How well is my process performing compared to what is expected by my customer?”
A high Cpk value signifies that your process is highly capable, meaning it can consistently produce output within the desired limits. This indicates a high probability that your process will produce products or services that meet customer requirements effectively, thus reducing the risk of defects or errors. In essence, Cpk provides a way to quantitatively express the level of process capability and allows for direct comparison between different processes or improvements over time.
Why is Process Capability Analysis critical in Six Sigma?
Process Capability Analysis (PCA) is the heart and soul of any successful Six Sigma initiative. It is a set of calculations used to determine how well a process can meet specification limits. By conducting PCA, you are effectively comparing the performance of your process against the voice of your customer.
The criticality of PCA in Six Sigma stems from its ability to assess how well the process meets customer requirements, which is a fundamental aspect of Six Sigma. It aids in identifying potential problem areas that might lead to deviations or defects in the final product or service. PCA, in a way, acts as a bridge between the statistical understanding of the process and the practical approach to reducing variations, thereby driving improvements and efficiencies.
Can a process be capable yet not meet customer requirements?
Indeed, it’s possible for a process to be statistically capable—producing outputs within the defined specification limits—but still fail to meet customer requirements. This can happen when there is a misalignment between what the process produces and what the customer needs.
For instance, if your process specifications are based on outdated data or incorrect assumptions, your process might be capable according to these specifications, but fail to satisfy your customers. This scenario underscores the importance of not just focusing on process capability but also continuously verifying that your process is aligned with the current and evolving customer requirements. Six Sigma champions always ensure that their improvements are driven by the voice of the customer to avoid such mismatches.
How does Six Sigma improve Process Capability?
Six Sigma’s main aim is to reduce variation and defects in a process, thereby enhancing its capability. This is achieved through DMAIC (Define, Measure, Analyse, Improve, Control), a structured problem-solving methodology.
In the Define phase, project goals and customer requirements are outlined. The Measure phase involves gathering data and assessing the current process capability. The Analyse phase identifies sources of variation. The Improve phase then implements changes to reduce variation and improve process capability. Finally, the Control phase ensures that these improvements are sustained over time.
By systematically reducing variations and defects, Six Sigma helps improve the process capability, ensuring that the process consistently meets or even exceeds customer requirements. This results in enhanced customer satisfaction, reduced costs, and improved bottom-line performance.
What’s the role of Six Sigma Master Black Belt, Black Belt, and Green Belt in Process Capability Analysis?
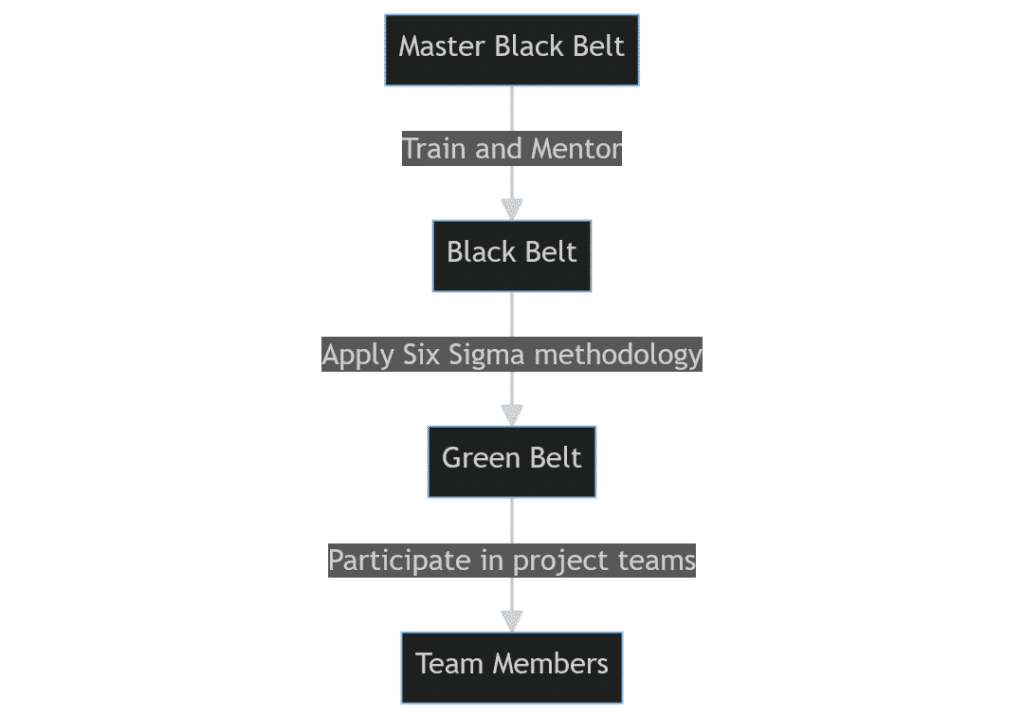
The Six Sigma hierarchy of Master Black Belts, Black Belts, and Green Belts each play an integral role in PCA.
- Master Black Belts are essentially the in-house coaches or trainers on Six Sigma. They provide direction for process capability analysis efforts, imparting knowledge, and ensuring the use of the right techniques to assess process capability. They also ensure that process improvements align with strategic business objectives.
- Black Belts work more on the ground. They apply the Six Sigma methodology to specific projects within the organisation. They perform process capability analysis to identify problem areas, root causes, and develop viable solutions to improve process performance. They are often project leaders who guide Green Belts and other team members.
- Green Belts apply Six Sigma tools to their daily work. They participate in project teams led by Black Belts and contribute to process capability analysis by collecting and analysing data, running experiments, and assisting in the implementation of improvements.
In a nutshell, each belt plays a key role in enhancing process capability, thereby driving the overall success of Six Sigma initiatives within the organisation.
Deep Dive: Process Capability Analysis Unpacked
Subscribe to our newsletter!
Unravelling Process Capability Analysis
PCA is a statistical tool in Six Sigma that assesses a process’s ability to meet customer requirements. It’s an assessment tool that helps you understand how well your process can churn out products or services within specified limits, defined by the voice of your customer.
PCA, essentially, provides you with a detailed report card of your process. It shows how the outputs of your process perform against the specification limits over a period of time.
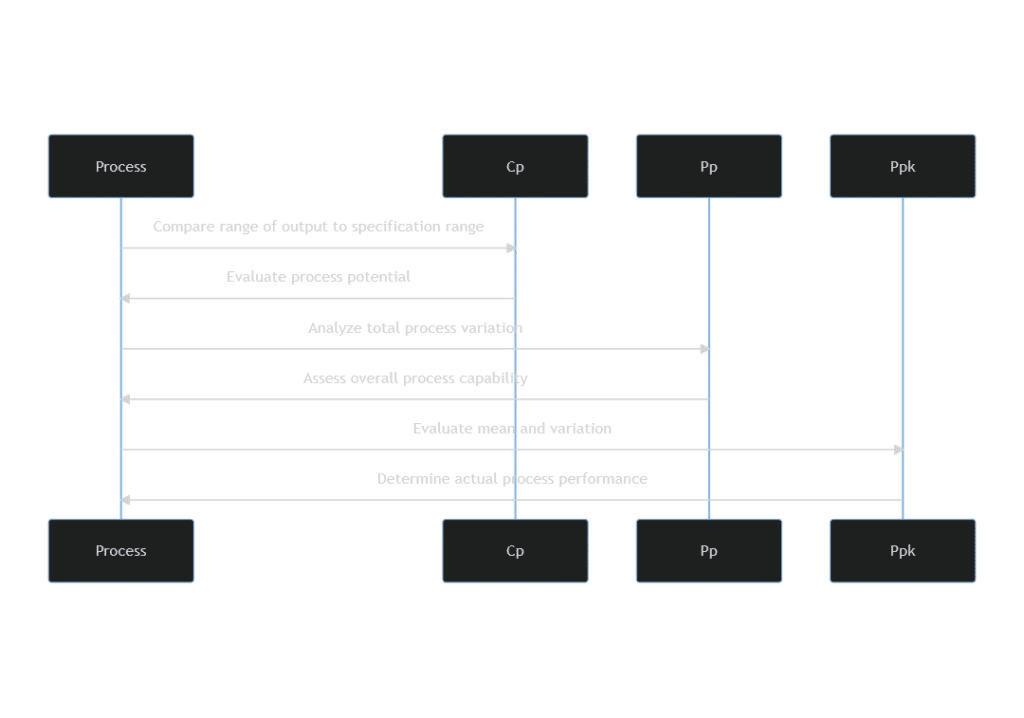
Process Capability Analysis: A Closer Look
The first step in PCA is to ensure your process is stable. Remember, a stable process is one that’s predictable and under statistical control. Once stability is ensured, we move on to measuring process capability.
Measurements typically include Cp, Cpk, Pp, and Ppk. Remember Cpk from earlier? It’s the Process Capability Index and tells us how well the process can meet two-sided specification limits. Pp and Ppk are similar indices that deal with overall process capability.
Through these measurements, we understand how our process is performing, and where we need to focus our improvement efforts.
The Crucial Role of Data in PCA
Data plays a vital role in PCA. It is essential to collect accurate and reliable data for an effective PCA.
Data should be collected over time and under normal operating conditions to ensure it represents your process accurately. This can be achieved using a data collection plan, which outlines what data to collect, how to collect it, and how often.
PCA: A Key Driver of Process Improvement
PCA provides valuable insights that help drive process improvements in Six Sigma. With PCA, you can identify sources of variability, understand their impact on your process, and target improvement efforts where they will have the greatest impact.
PCA is a powerful tool that can help you increase process consistency, reduce defects, and ultimately enhance customer satisfaction.
There are a few different measures of process capability, and each has its own formula. The two most common measures are Cp and Cpk. Here are the formulas for both:
- Cp (Process Capability Index): Cp is used to calculate the potential capability of a process to meet specifications. The formula for Cp is as follows:
- Cp = (USL – LSL) / 6σwhere:
- USL = Upper Specification Limit
- LSL = Lower Specification Limit
- σ = Standard Deviation of the process
- Cp = (USL – LSL) / 6σwhere:
- Cpk (Process Capability Index): Cpk is used to assess the ability of a process to meet specifications considering both the process mean and variability. The formula for Cpk is:
- Cpk = min [ (USL – μ) / 3σ , (μ – LSL) / 3σ ]where:
- USL = Upper Specification Limit
- LSL = Lower Specification Limit
- μ = Process Mean
- σ = Standard Deviation of the process
- Cpk = min [ (USL – μ) / 3σ , (μ – LSL) / 3σ ]where:
Note: The above formulas assume that the process data follows a normal distribution. If the process data does not follow a normal distribution, alternative methods may need to be used.
Unveiling Cp, Pp, and Ppk
Cp, Pp, and Ppk are statistical measures that provide insights into the capability of your process, each offering a slightly different perspective. Let’s break these down.
Understanding Cp: Process Capability Index
Cp, or the Process Capability Index, measures a process’s potential by comparing the range of output to the range of allowable values specified by the customer. In simpler terms, Cp assesses the capability of a process assuming it is centred between the specification limits.
The Cp value provides insights into the spread of the process distribution compared to the spread of the specification limits. A higher Cp means the process spread is less than the specification spread, indicating a more capable process.
It’s important to remember that Cp is a theoretical measure of process capability and assumes that the process is perfectly centred. In real-world scenarios, this may not always be the case.
Exploring Pp: Overall Process Capability
Pp, or Overall Process Capability, is another measure of process capability. Like Cp, it compares the range of output to the allowable specification range. However, unlike Cp, Pp considers both within and between subgroup variation.
Pp is a long-term analysis measure, useful when you’re looking at a process over an extended period. Pp gives you a broader view of your process performance, including shifts and drifts in the process mean over time.
Getting to Know Ppk: Process Performance Index
Ppk, or the Process Performance Index, measures how well a process is performing relative to its specification limits, considering both the average and variation of the process. It takes the process’s actual performance, including its average or centering, into account.
A high Ppk indicates a well-centred process that produces output within specification limits, thereby satisfying customer requirements. It provides a more realistic picture of your current process capability, making it extremely valuable in Six Sigma projects.
In conclusion, Cp, Pp, and Ppk are all integral to the analysis of process capability in Six Sigma. Understanding these measures provides a robust foundation for driving process improvement and achieving excellence.
Wrapping Up: Mastering Process Capability Analysis in Six Sigma
Now, let’s tie all this knowledge together and see how it applies in the real world.
The Power of Process Capability Analysis
PCA is more than just a statistical tool; it’s a key driver of process improvement. By analysing process capability, Six Sigma professionals can identify potential problem areas, pinpoint sources of variability, and focus their improvement efforts effectively. With PCA, you can not only improve process consistency and reduce defects but also enhance customer satisfaction.
A Closer Look at the Six Sigma Hierarchy
Remember, in the Six Sigma hierarchy, Master Black Belts, Black Belts, and Green Belts each play a significant role in PCA. They use PCA to ensure that their process improvements align with strategic business objectives and meet customer requirements.
The Role of Key Statistical Measures
Cp, Cpk, Pp, and Ppk are critical measures in PCA. These indices help us understand the capability of our processes, providing insights into the process spread, centering, and overall performance against specification limits. Understanding these measures is fundamental to driving process improvement in Six Sigma.
Data: The Fuel for PCA
Never forget the importance of data in PCA. Accurate and reliable data, collected over time under normal operating conditions, is the fuel that drives PCA. With a robust data collection plan, you can ensure your PCA accurately represents your process and provides valuable insights for improvement.
The Path Ahead: Continuous Improvement
Learning about PCA is a big step in your Six Sigma journey, but it’s just the beginning. Remember, Six Sigma is all about continuous improvement. Always be ready to reassess your process, collect new data, and re-analyse your process capability. The journey to process perfection never ends, but every step brings you closer to your goal.
Subscribe to our newsletter!